Innomac Formwork
Our Machineries
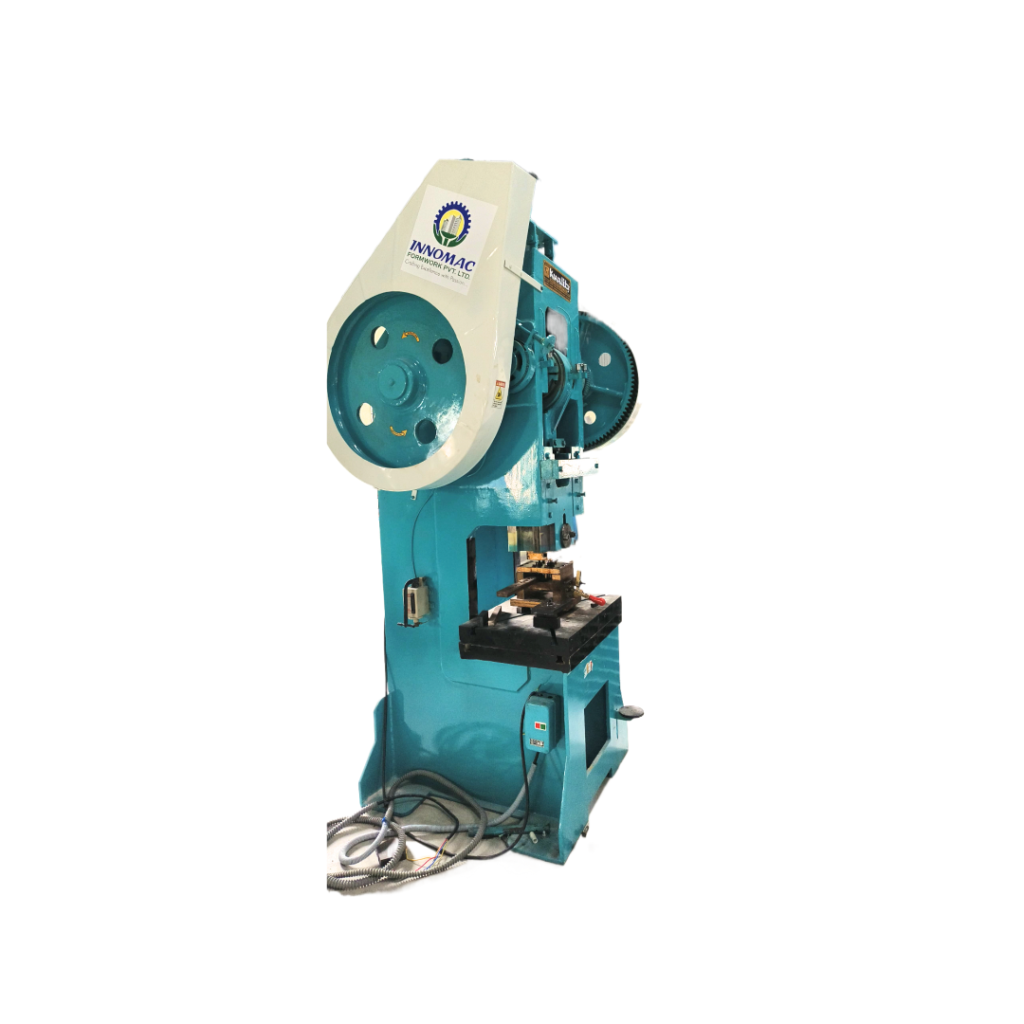
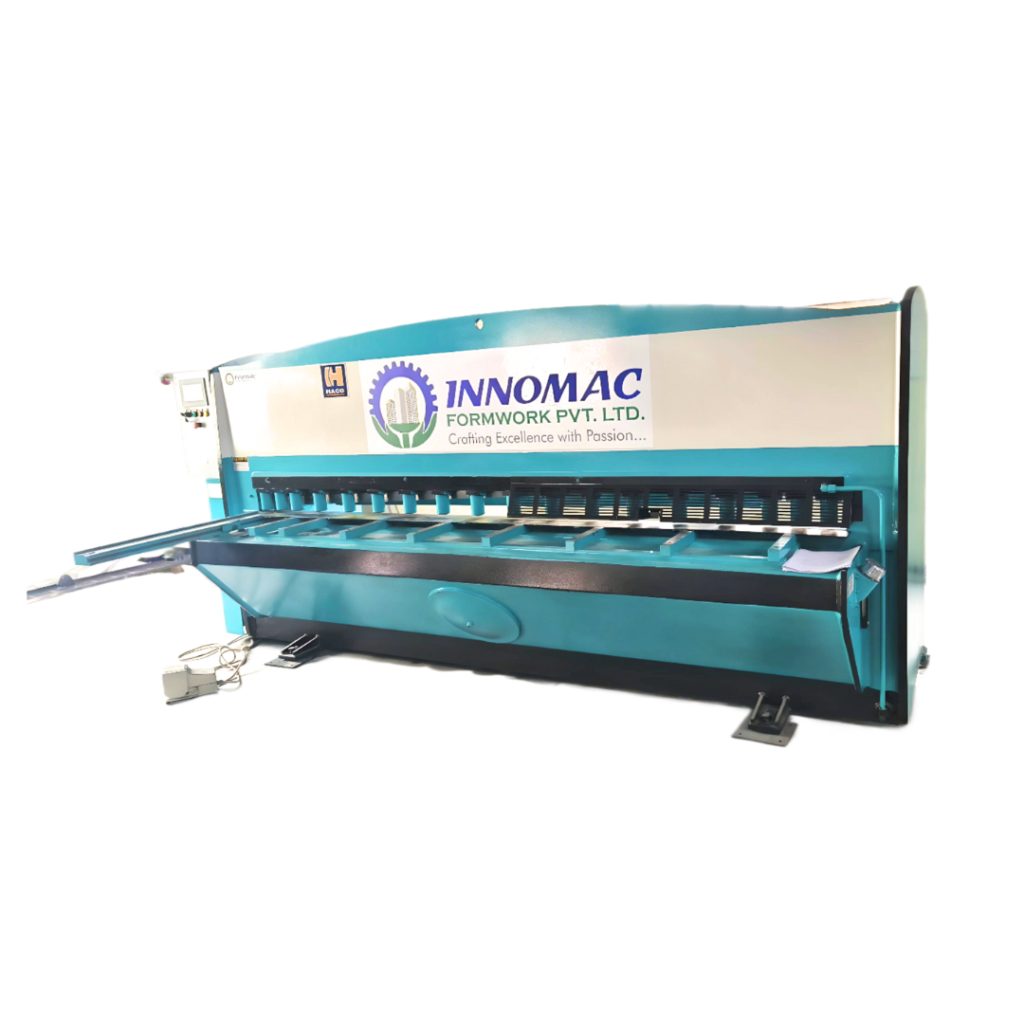
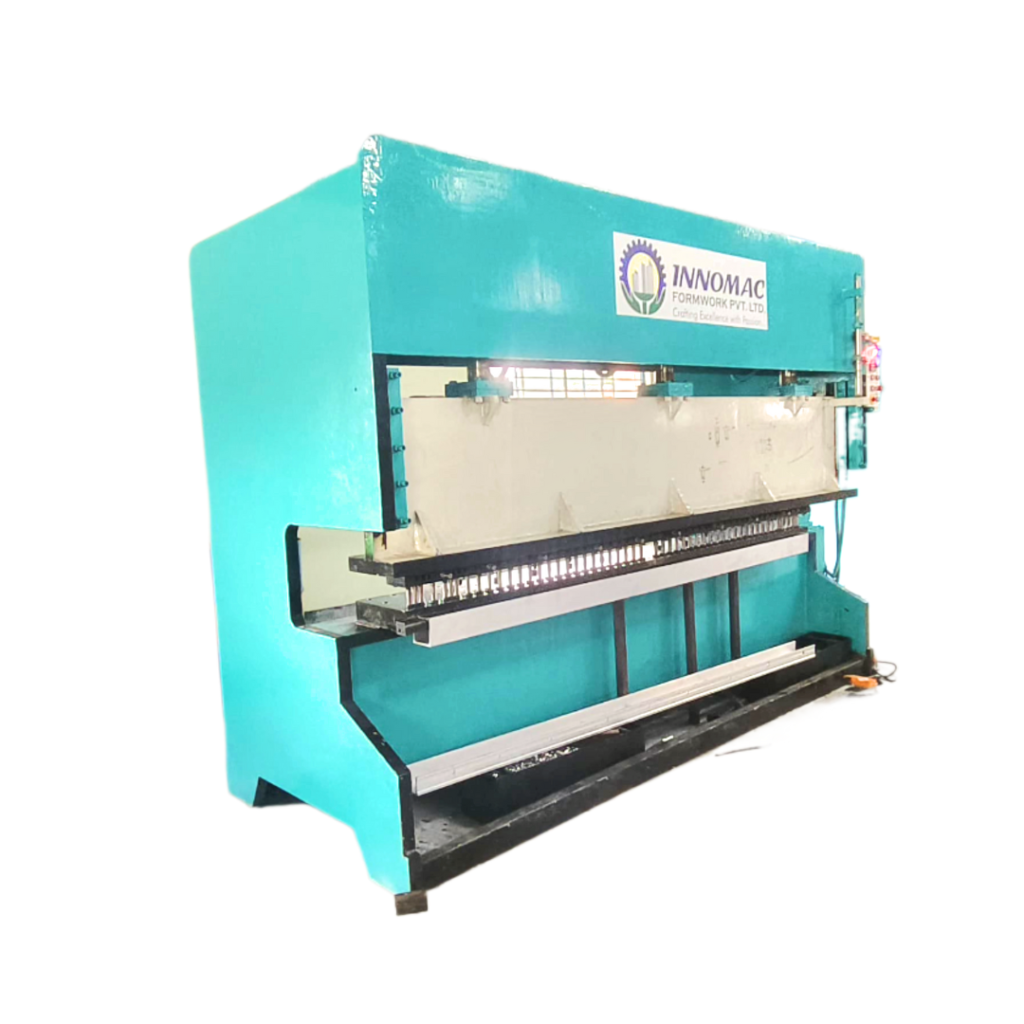
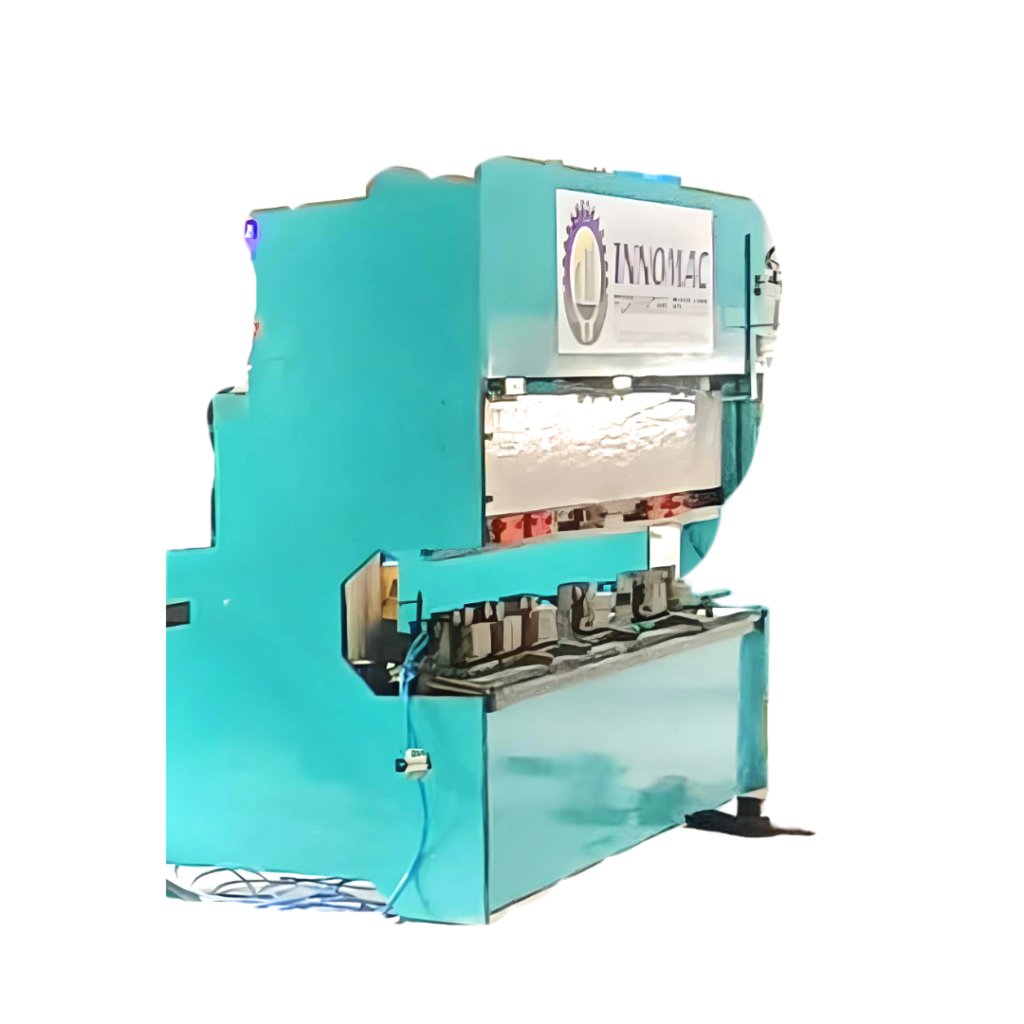
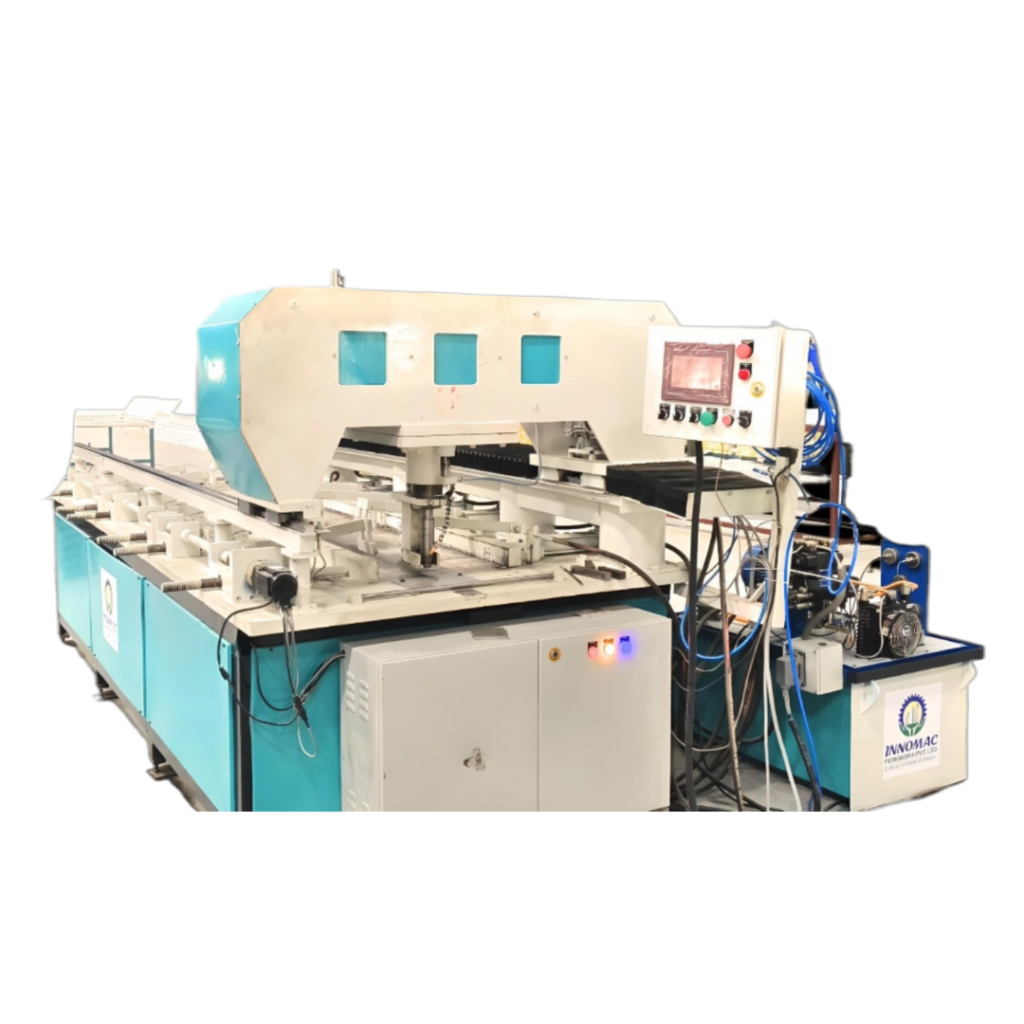
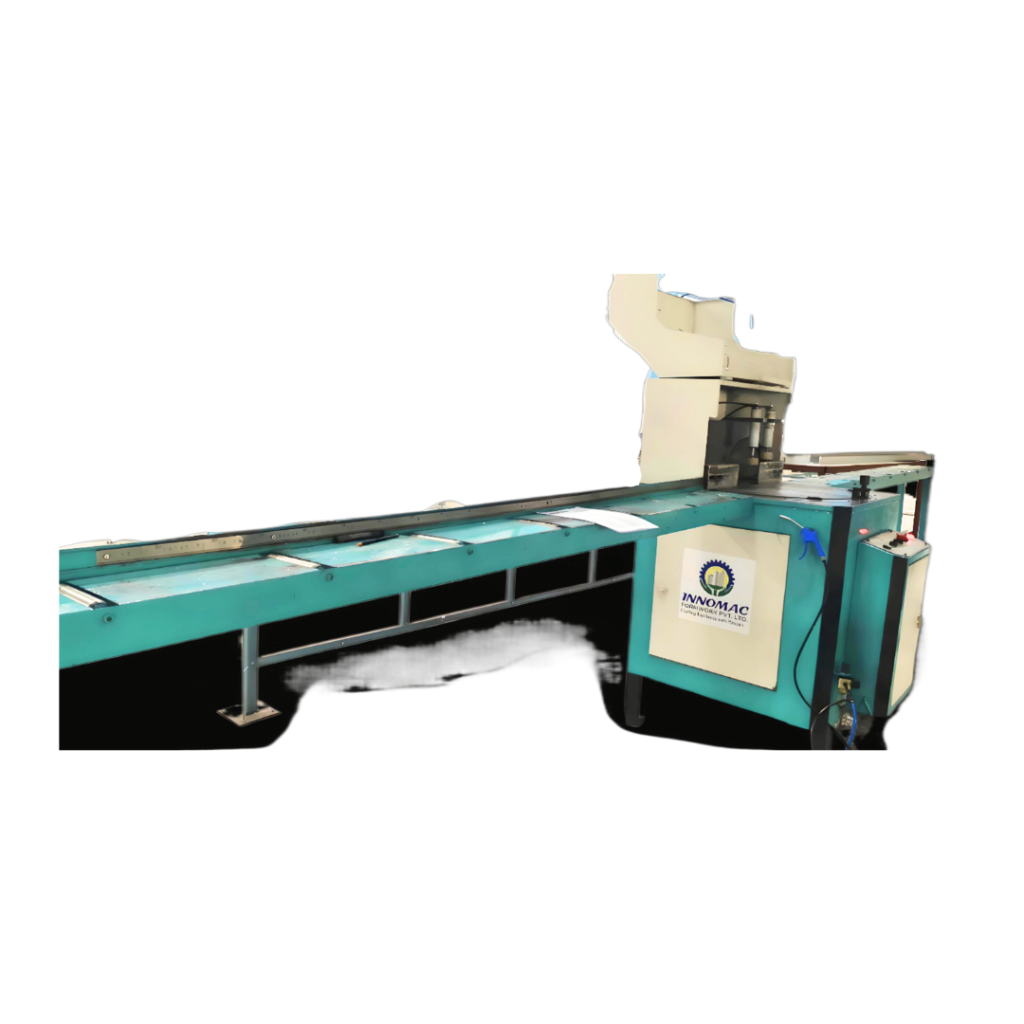
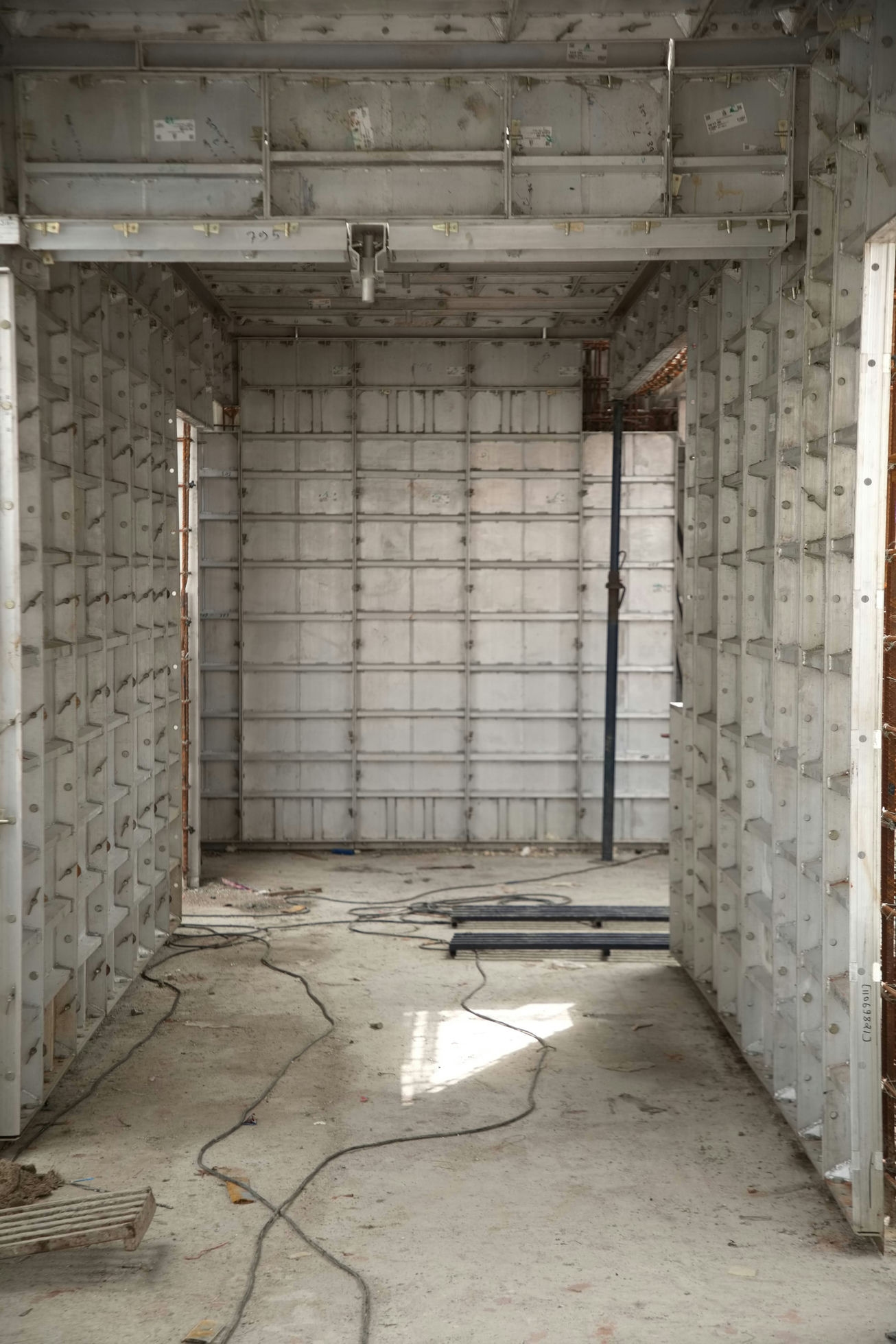
INNOMAC ALUMINIUM FORMWORK
INTRODUCTION
SHELL DRAWING DESIGN
MODULATION DRAWING DESIGN
Site will be provided with a set of formwork drawings as the followings;
Aluminum formwork layout plan, elevation drawings and 3D model indicating the general arrangement, location of formwork components and its accessories.
Formwork support system, formwork slab and connection details
Location of weep holes, inspection opening, formwork opening for transfer formwork, concreting hole, etc.
FEATURES:
Construction Speed
Reduced Material Wastage
Easy to Handle
More Repetitions
Higher Structural Strength
Reduced Labour Cost
Higher Salvage Value
Increased Carpet Area
Higher Seismic Resistance Structure
Leakage Resistance Structure
PREPARATORY WORK PACKAGE & STORAGE
Prepare field for goods stacking
formworks for each block, should prepare fields where are the nearest to this block for goods stacking in advance, it makes crane work convenient.
Note: it's about 300 m² of aluminum formwork per truck, covers an area of 80m²
WALL FORMWORKS ASSEMBL
The vertical formwork is generally nailed by one set of pin wedge per 300mm, and the horizontally stitched formwork end pin must be nailed, the pin is placed from top to bottom to avoid shaking when vibrating the concrete and the internal and external walls are to be held together by Flat-Tie. The installation procedure:
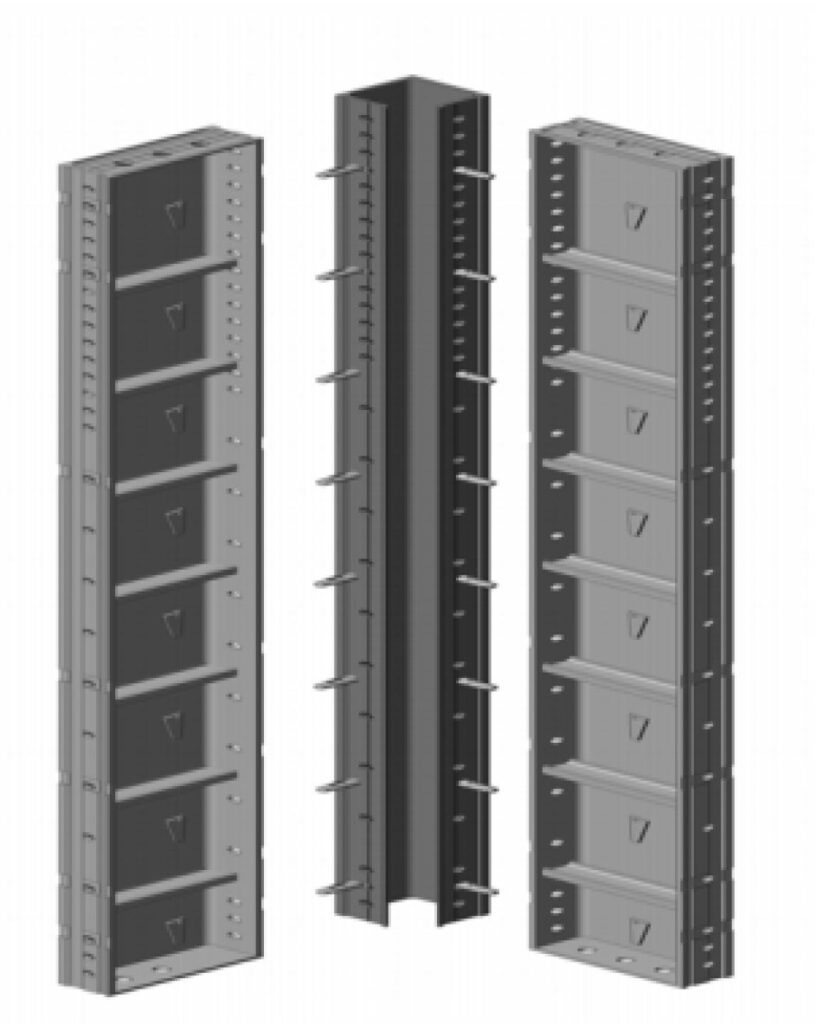
Install the inner wall formwork form the inner corner
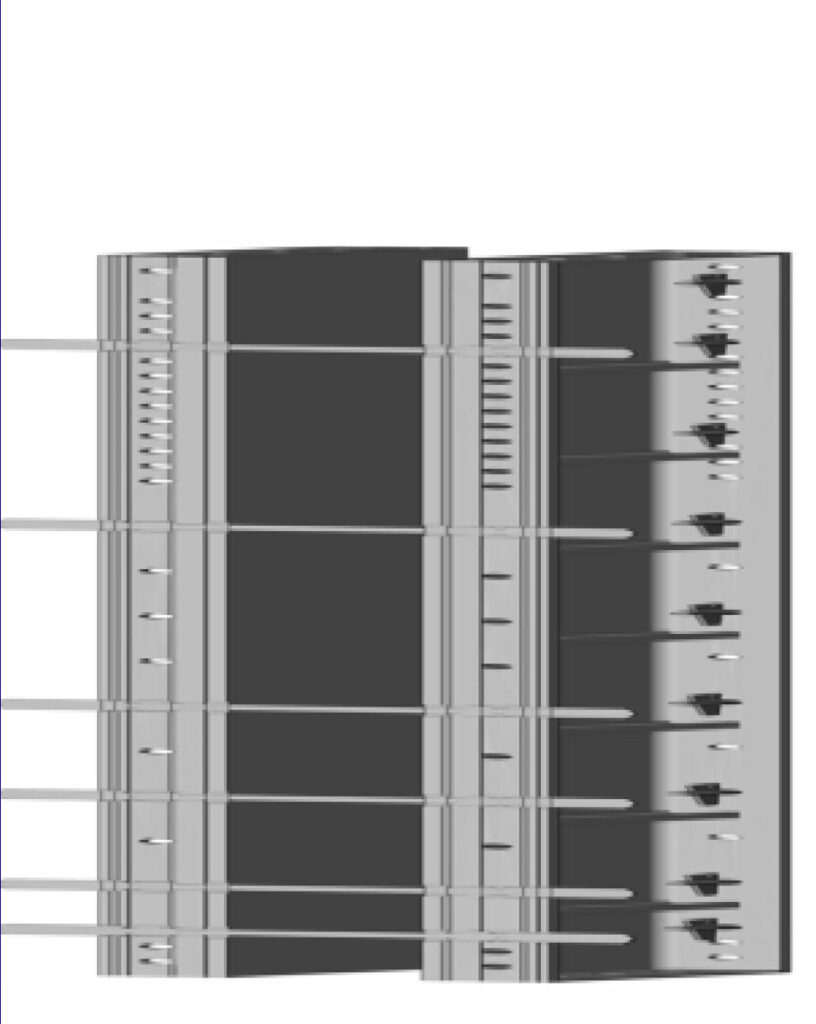
Install Flat Tie
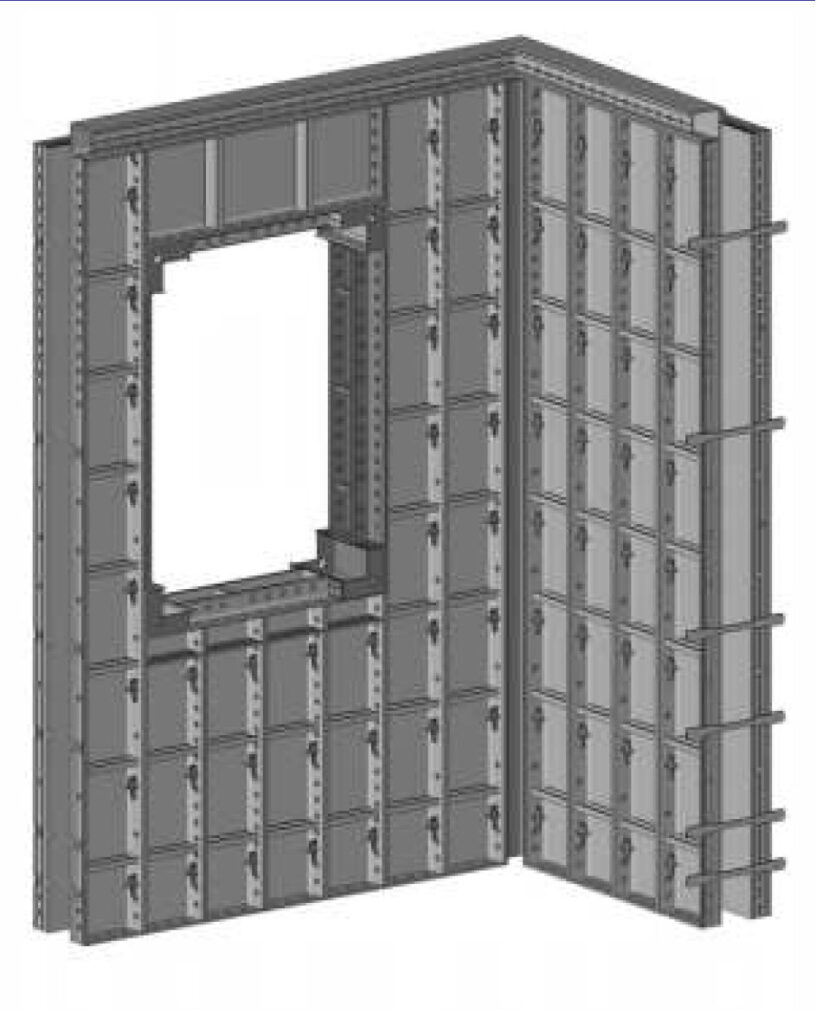
Install external wall formworks
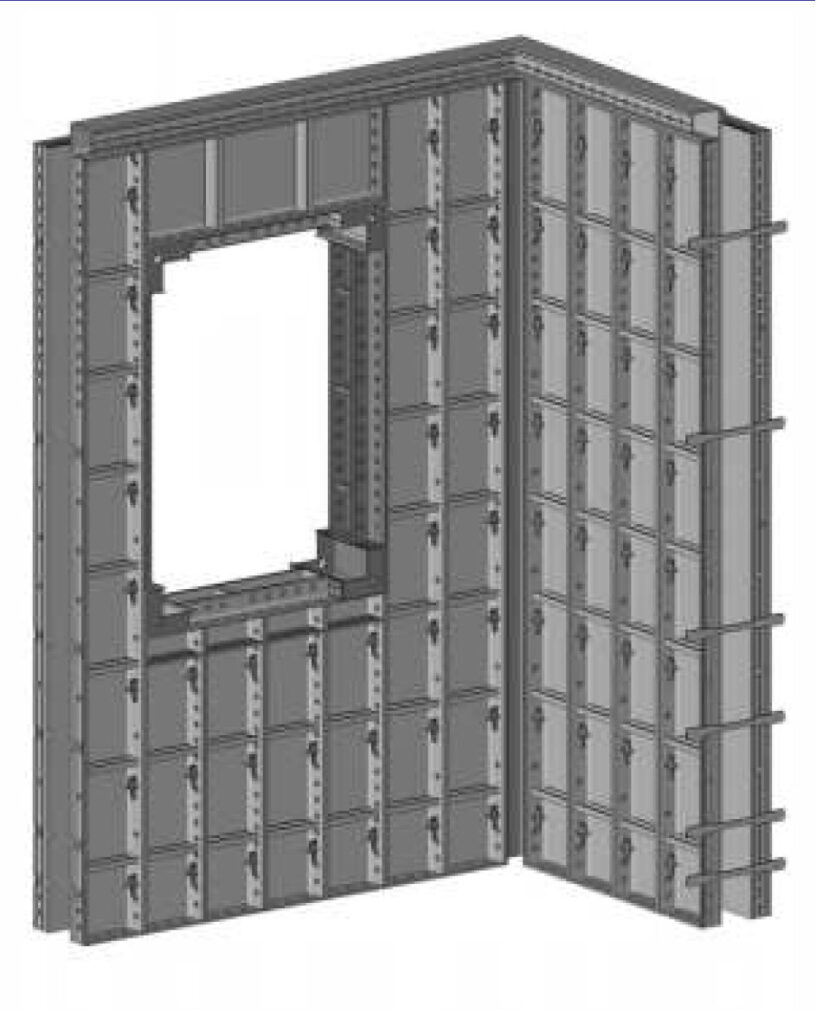
Repeat the step 1 to 3 and connected all the formworks with wedges and pins
International Technique
Incorporating cutting-edge software such as Staad Pro, Revit, and Autocad, we have revolutionized the designing and drawing process, providing real-time design solutions that outperform conventional methods. With these advanced tools, we can swiftly analyze and optimize structures, ensuring precision and efficiency throughout the design phase. Our topmost priority is the safety of Formwork and the overall structure. Through meticulous attention to detail, our designs prioritize stability, durability, and adherence to industry standards, guaranteeing safe and reliable construction outcomes.
High end Finishing
Innomcformwork System utilizes components manufactured from extruded Aluminium alloy, ensuring that the dimensions adhere to strict tolerances of no more than 2mm. This precision in manufacturing guarantees a high level of accuracy during assembly, contributing to the system’s overall stability and ease of installation.
Moreover, the smooth surface of Aluminium plays a vital role in enhancing the concrete finish. The exceptional surface quality minimizes the need for plastering activities, saving both time and resources during the construction process. This results in a superior aesthetic appearance and a cost-effective solution for various building projects.
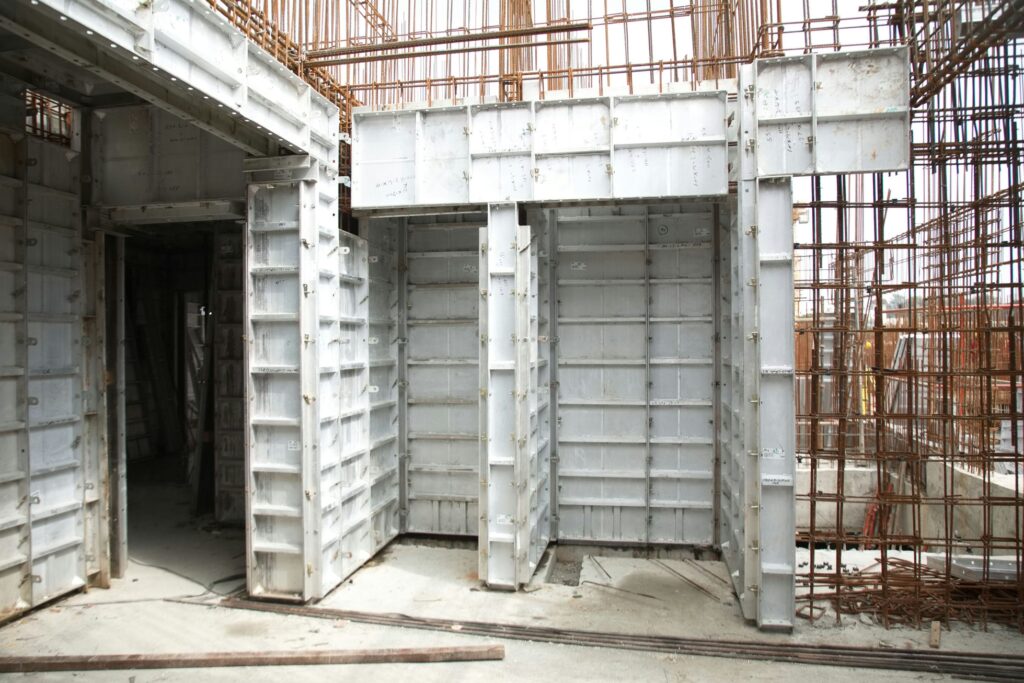
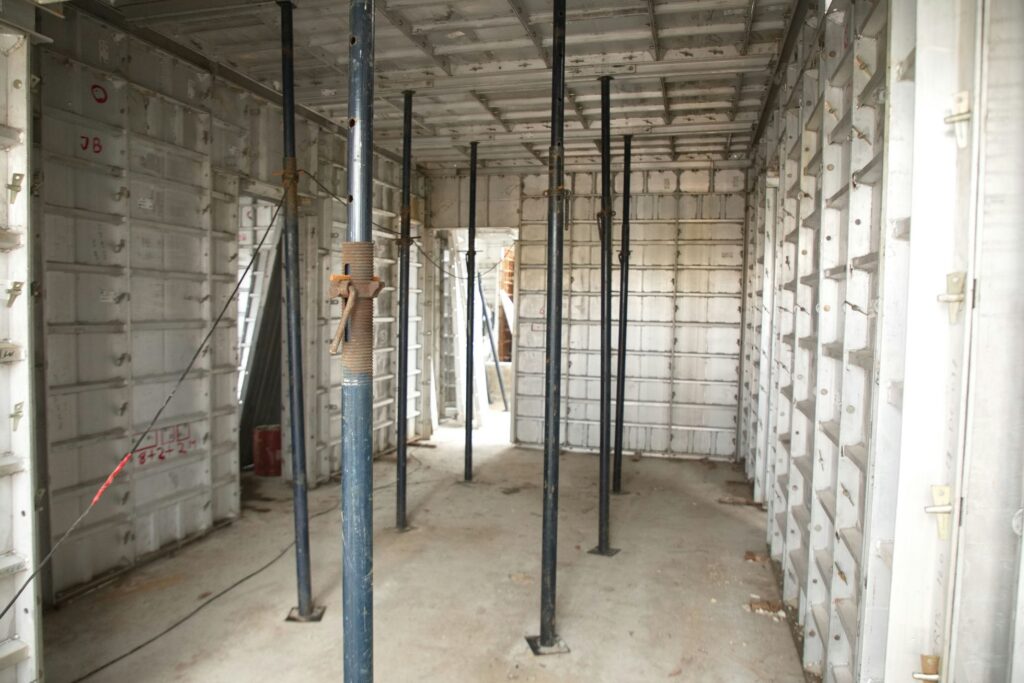
Less inventory and economical
With the innomac Aluminium Formwork system, the slab and beam can be safely stripped after three days, depending on the concrete strength achieved. This efficient process leaves the props head intact, along with the props, providing essential support to the structure.
Additionally, walls and columns can be de-shuttered after just twenty-four hours, thanks to the system’s design and the quality of the materials used. This early stripping capability significantly reduces the need for excessive inventory and parts handling, resulting in a substantial cost reduction. The streamlined workflow and accelerated construction pace offered by the system translate to improved project timelines and enhanced cost-effectiveness, making it an ideal choice for various construction projects.
High repetition and durability
The innomac Aluminium Formwork system is backed by state-of-the-art technology, ensuring the manufacturing of all its components to the highest standards. The system utilizes Aluminium alloy 6061, a top-quality material known for its exceptional properties. One key advantage of this alloy is its impressive tensile strength, which enables it to withstand significant pressure and forces.
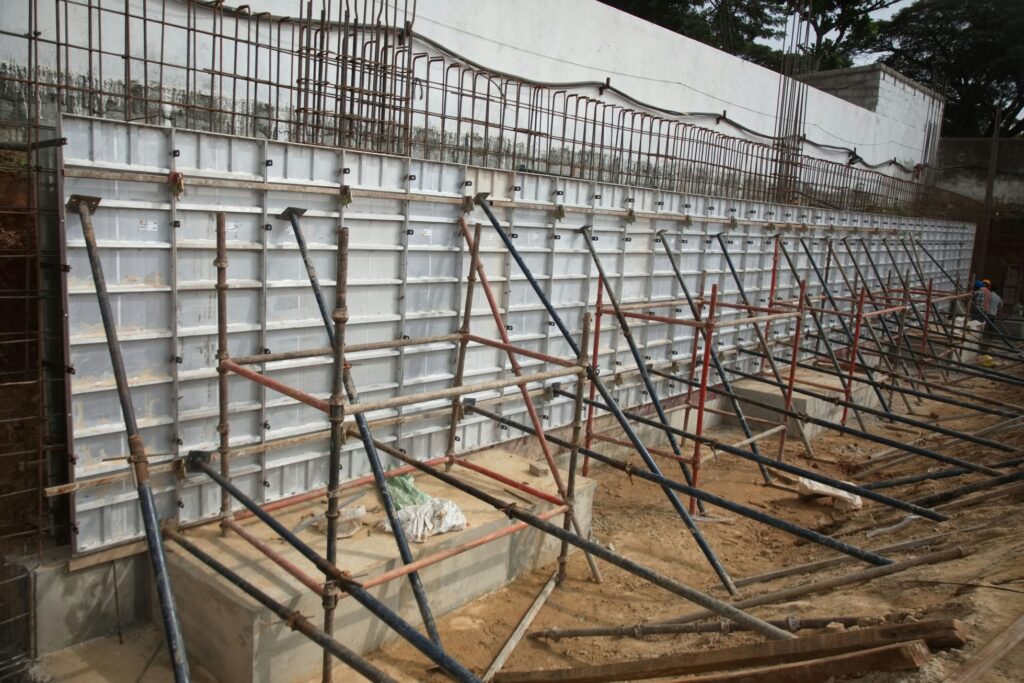
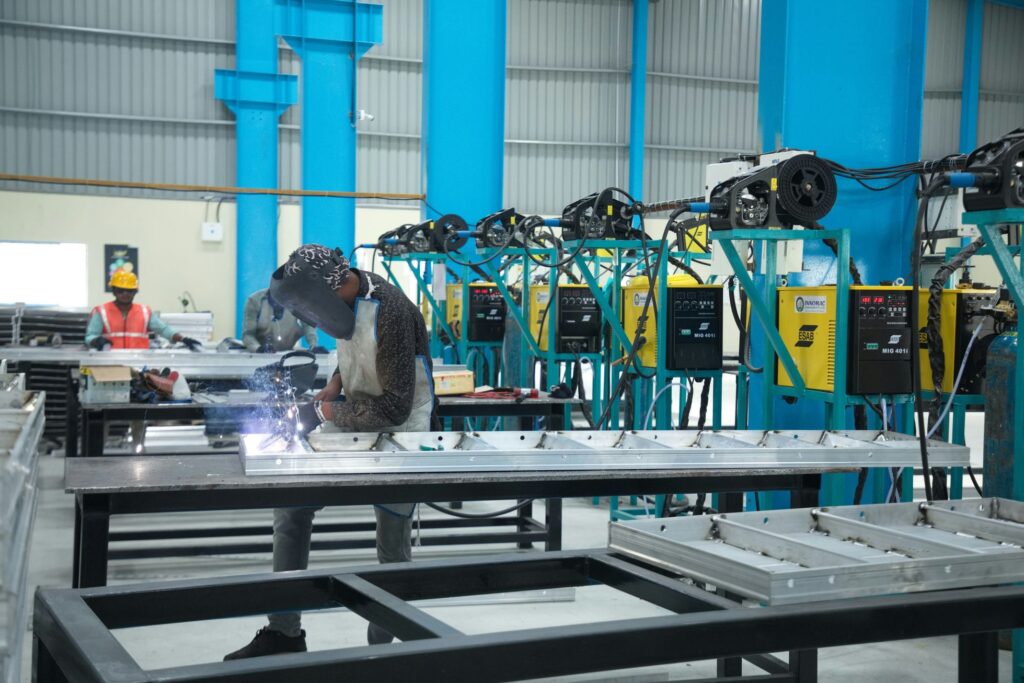
Safety of Workers
Moreover, the system’s well-defined number of props plays a crucial role in facilitating quick and safe assembly. The props provide essential support to the formwork and structure, ensuring stability during construction. The clear guidance on the number of props needed for each project eliminates guesswork and ensures the correct setup, further enhancing safety and efficiency on the construction site.
Eco-Friendly
The absence of wood ensures that no wood grain or imperfections transfer onto the concrete surface, resulting in a smooth and aesthetically pleasing finish. The Aluminium Formwork system provides an excellent concrete surface appearance without the need for additional plastering or finishing work, saving time and resources during the construction phase.
Moreover, the use of Aluminium also enhances the system’s durability and longevity, as Aluminium is resistant to corrosion and can withstand various weather conditions. Its lightweight nature further facilitates easy handling and installation, optimizing construction efficiency.
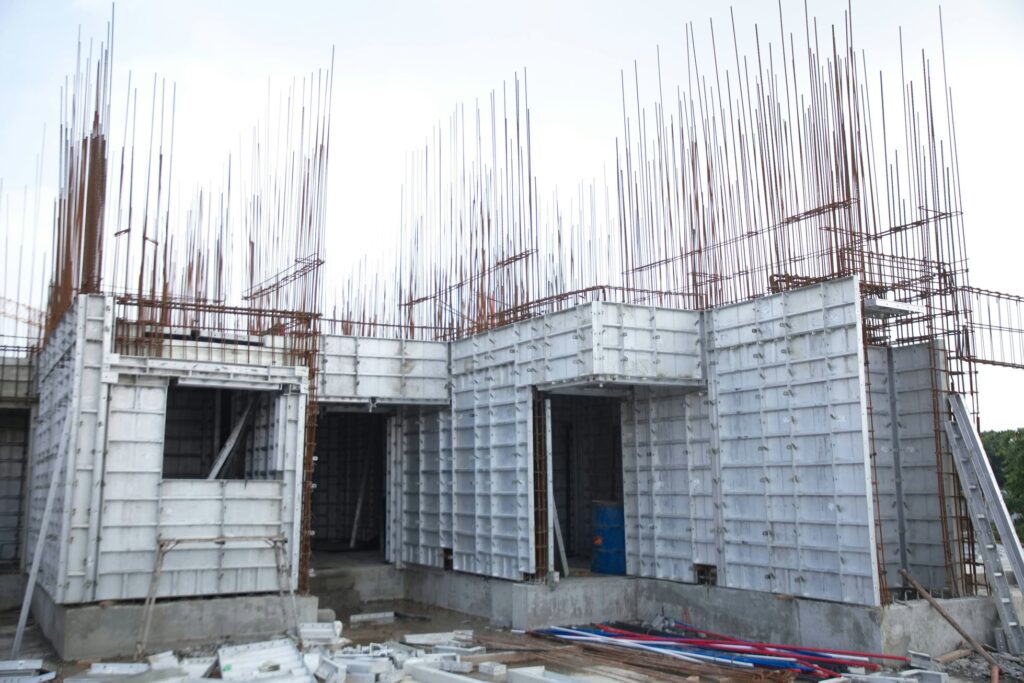
Innomcformwork Wind Screen offers a secure working platform suitable for any height, functioning as a crane-dependent climbing system that comprises four levels of working platforms. Its design features a seamless enclosure that safeguards site crew from fall hazards, wind, and adverse weather conditions.
To ensure protection against dropped objects, the system incorporates horizontal and vertical sealing, even during lifting operations. Additionally, it can adapt to various layout shapes, making it versatile for different construction scenarios. The working platforms can be easily relocated to accommodate non-constant storey heights, further enhancing flexibility and efficiency.
The inclusion of a suspended platform at the bottom helps seal tie rod holes and wall tie slots, resulting in higher productivity and instilling a stronger sense of safety among workers. Overall, the Innomcformwork Wind Screen system prioritizes safety, productivity, and adaptability, making it an optimal choice for construction projects at various heights and layouts.
The Innomcformwork Deck System proves highly efficient in achieving a rapid 3-4 day slab cycle for typical projects. With an impressive shuttering speed of approximately 350 sq. ft. per man hour and de-shuttering at 650 sq. ft. per man hour, the system streamlines the construction process, saving valuable time and labor costs.
One significant advantage of the Innomcformwork Deck System is its minimal number of components, making it particularly advantageous for projects carried out at great heights. This simplifies the assembly process, reduces complexity, and enhances overall safety during construction.
Moreover, the panels’ automatic wind locking feature ensures secure fastening during assembly, which is of paramount importance when working at elevated heights. This additional safety measure adds peace of mind to workers and further protects against potential hazards.
In summary, the Innomcformwork Deck System offers a winning combination of speed, efficiency, and safety, making it an excellent choice for projects that require rapid slab cycles, particularly in challenging construction environments.
Some of the key features are-
• The Innomcformwork Deck System boasts several key features that make it a versatile and efficient choice for construction projects:
• The system’s modular design allows for easy expansion and reduction to accommodate changes in slab heights and areas, providing flexibility in construction planning.
• Safe erection and stripping from the floor below enhance worker safety and streamline the construction process.
• The panels of the system can be removed without disturbing props or concrete, allowing for convenient adjustments during construction.
• Automatic wind locking of panels during assembly is especially crucial in areas prone to high winds, ensuring the stability of the structure.
• The system can be erected in multiple directions simultaneously, further enhancing construction efficiency.
• No “x” bracing is required, simplifying the setup and reducing the need for additional support elements.
• The interlocking mechanism between the main components, Panels & Props, ensures stability against strong wind loads.
• Despite its sturdy construction, the system’s components are designed to be lightweight, allowing for easy handling by just two workers.
• Telescopic, Side, and End Filler Beams simplify shoring around columns and other interruptions, making construction more efficient and cost-effective.
• Non-welded components ensure the system’s structural integrity and ease of maintenance.
• The durability of the system’s components guarantees long-lasting performance, contributing to its longevity and value.
• Overall, the Innomcformwork Deck System’s combination of innovative features makes it an excellent choice for construction projects that demand adaptability, safety, and cost-efficiency.
Indeed, Innomc Wall Formwork has its origins in the use of squared timbers and boards. This traditional approach has led to the development of modern modular systems, known for their versatility and durability, allowing for a wide array of applications and extended service life in construction.
There are two main types of Innomc Wall Formwork based on their construction methods: girder Innomc Wall Formwork and panel formwork.
Wall Formwork
Absolutely, the girder wall formwork is a highly versatile and adaptable system in the realm of concrete construction. In this method, the formwork girders provide support for the form lining, while steel profiles serve as walers to reinforce the structure. This combination of components allows for efficient construction, especially in scenarios involving complex shapes and high loads.
One of the significant advantages of the girder wall formwork is its ability to be individually tailored to accommodate intricate designs and challenging construction requirements. This adaptability makes it an ideal choice for creating architectural concrete structures that demand precise and high-quality surface finishes, as well as specific anchor patterns.
Panel Formwork
Indeed, panel formwork is a highly efficient and practical solution for large-scale concrete construction projects. It is characterized by its simplicity and ease of use, primarily due to the following features:
Fewer Individual Components: Panel formwork systems consist of frames made of steel or aluminum, resulting in considerably fewer individual components compared to other formwork methods. This streamlined design simplifies the assembly and disassembly process, saving time and labor during construction.
Fixed Panel Sizes with Formlining: The panel formwork system features fixed panel sizes that come equipped with integrated formlining. This ready-to-use setup eliminates the need for additional surface treatments and speeds up the forming process for large areas.
We are a prominent organization in the construction domain, offering a wide range of Column Formwork solutions. Our formwork is crafted using heavy cast iron or stainless steel alloy, ensuring durability and reliability for various construction projects, including buildings, bridges, and offices. The formwork exhibits excellent resistance to acids and alkalis, enhancing its longevity and performance.
Our Column Formwork systems are designed to be modular, allowing for quick assembly and erection on-site, thereby reducing labor and crane time. The forms, made of steel or aluminum, sometimes supplemented with a timber form-face liner, can be adjusted on-site to accommodate different column sizes. Depending on the desired concrete finish, the forms offer various internal surfaces.
Metal formwork systems often feature integrated concreting platforms equipped with guard rails and access equipment, such as ladders, which minimizes the need for separate access provisions. Some systems incorporate integral props to stabilize the column formwork, further optimizing construction efficiency.
The metal forms are not only easy to clean and maintain but also generate minimal waste compared to traditional formwork methods, making them environmentally friendly and cost-effective.
For circular columns, we offer an alternative solution with disposable formwork, which comprises cardboard tubes with plastic liners. These formwork elements are left in place until the concrete gains sufficient strength, after which the cardboard is carefully removed.
In cases of disposable formwork, separate working platforms for concreting must be erected to access the top of the column.
With our diverse range of Column Formwork solutions, we aim to meet industry standards and deliver efficient, flexible, and environmentally conscious construction solutions for our valued clients.
Innomc Formwork Deck is a highly efficient hand-set panelised slab Formwork system designed to cater to various slab construction requirements with its three versatile Forming methods. This unique system can be adapted to suit virtually any slab job, streamlining the construction process by using the same set of parts across different configurations, thereby minimizing assembly errors.
Safety and ease of assembly are prioritized in the Innomc Formwork Deck system, thanks to the predefined number of Props required by the system. This ensures structural stability and quick assembly, reducing construction time and labor costs.
Overall, the Innomc Formwork Deck Formwork system offers a comprehensive and adaptable solution for slab construction projects, enhancing efficiency, safety, and convenience on the construction site.
The Decking System offers a range of salient features that make it a highly efficient and user-friendly solution for slab construction:
1. Fewer Components: The system is designed with fewer components, simplifying the assembly process and reducing the chances of errors during setup.
2. Integrated or Separated Facing: The system provides the flexibility to use integrated or separated facing, catering to various project requirements and finishes.
3. Minimized Compensation Area: The system minimizes the need for additional compensation, optimizing material usage and reducing waste.
4. Suitable for Any Slab Height or Thickness: It can be easily adapted to accommodate different slab heights or thicknesses, making it versatile for various construction projects.
5. Early Stripping: The system allows for early stripping, enabling a fast pour cycle and speeding up the construction timeline.
6. Safe De-shuttering: The system facilitates safe de-shuttering, preventing damage to the formwork materials and the structure during the removal process.
7. Low Number of Props: With a minimal number of props required per square meter, larger profile sections can be used, and the distance between props can be increased, enhancing efficiency and reducing support requirements.
8. Fair Finish Surface: The Decking System offers a smooth and fair finish surface, eliminating the need for additional plastering work.
9. Crane-Independent: The system does not depend on cranes for assembly or disassembly, providing flexibility in construction logistics.
In summary, the Decking System stands out as a highly effective solution for slab construction due to its ease of assembly, adaptability, early stripping capabilities, and the ability to achieve a quality finish without the need for plastering. Its user-friendly design and efficient components make it a preferred choice for a wide range of construction projects.
Salient Features of Innomc Formwork Deck, the Decking System by Maxformwork:
1. Quality Manufacturing: Maxformwork is a leading manufacturer in the formwork industry, committed to producing high-quality systems like Innomc Formwork Deck. The manufacturing facilities in Rudrapur and Delhi are equipped with state-of-the-art technology to ensure precision and excellence in every component. Each part of Innomc Formwork Deck undergoes rigorous quality checks during production.
2. Closed Hollow Profile: Innomc Formwork Deck pioneered the use of closed hollow profiles, which offer superior stability and robustness in lateral torsional buckling compared to open profiles. The closed design prevents concrete from getting trapped, resulting in an improved concrete finish and reduced cleaning effort.
3. Lightweight and Sturdy Panels: Innomc Formwork Deck panels are designed to be lightweight yet sturdy, allowing for easy handling by a single worker. The ergonomic grip profile further enhances convenience during assembly, making it possible to construct large slab areas manually.
4. Advanced Design Software: Maxformwork employs cutting-edge software, such as Staad Pro, Revit, and AutoCAD, for designing and drawing. This real-time design solution replaces conventional methods, enabling precise and efficient formwork designs. Safety is a top priority in their designs, ensuring the utmost protection for both the formwork and the structure.
5. Rigorous Testing: Each component of Innomc Formwork Deck undergoes thorough testing at the state-of-the-art laboratory at IIT Chennai. The products are tested both individually and as a complete system to understand their load capacity and failure patterns, ensuring the utmost reliability and performance.
6. Early Deshuttering Facilitation: Innomc Formwork Deck allows for early deshuttering of slabs without disturbing the props. To ensure the safe implementation of this feature, Maxformwork provides detailed design calculations and Staad models not only for Innomc Formwork Deck but also for the deshuttering process.
In summary, Innomc Formwork Deck stands out as a high-quality and innovative formwork system, offering exceptional features such as closed hollow profiles, lightweight yet sturdy panels, advanced design technology, and comprehensive testing. The system’s ability to facilitate early deshuttering while ensuring safety showcases its efficiency and effectiveness in modern construction projects.